Making countertops from artificial stone with your own hands
For kitchen and bathroom furniture, reliability and functionality are very important. And ease of cleaning is also required - it is imperative to monitor cleanliness. An artificial stone countertop meets many of these criteria. But you need to choose the right material so that it doesn't turn out that an expensive thing does not live up to expectations.
The content of the article
Types of artificial stone
Recently, there has been a growing trend towards the use of more natural materials in decoration. The same countertop in the kitchen or bathroom. Let MDF be a good option, but you want something more reliable and solid. The most optimal choice is natural stone. But this option is too expensive. A more budgetary countertop made of artificial stone, although it is very difficult to call it natural. Only one of the types, and then with a stretch.
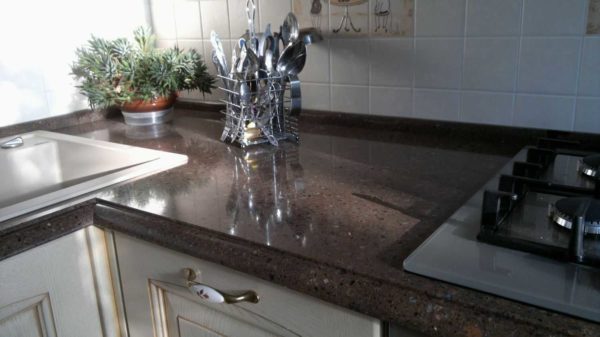
The artificial stone countertop looks good. It is important that it is also convenient in operation and "long-playing"
When familiarizing with the topic, it turns out that artificial stone can be different. And radically different - from different materials with different properties. Or they use different technologies, for example, injection molding. This is how seamless worktops of any shape are made. Or they stick sheet material on the base, but here you can't do without seams.
But don't jump to conclusions. A seamless countertop seems to be better. Maybe. But with injection technology, plastic is used, and it is prone to scratches. So well finished seams are better. With a high quality of work, they do not affect the complexity of cleaning, but are noticeable only from a close distance. In general, we are dealing with the technologies for the production of artificial stone countertops.
Acrylic countertops
Seamless countertops are made of acrylic stone. It is a plastic that is sold in liquid form. The composition can be mixed with natural stones or sand, but the bulk is, after all, plastic with all its advantages and disadvantages. Such material can be called liquid stone, liquid marble, etc. The essence does not change. Unless this name hides an agglomerate. But here it is necessary to clarify the percentage of the mineral component. If it is less than 90%, and acrylic is used as a binder, then, whatever one may say, it is an acrylic tabletop, not a stone one.
Advantages - a variety of colors, composition options, a low price (if this is without frantic markups). Disadvantages - the surface is scratched, afraid of the hot. After scratches appear, they can be polished, but this is not a cheap service. After recovery, the species will recover for a while. But for a while - this is until new scratches appear.
The technology for making acrylic stone countertops is simple. Formwork is made according to the specified dimensions and shape. Acrylic is poured into it, they wait until the final hardening. The formwork is removed. Further, in theory, it is necessary to wait until the hardening processes finally end. This is about two weeks. During this time, all volatile components will evaporate from the plastic, it will gain maximum strength. But firms that produce cast countertops, most often, skip the aging stage. This is both time and cost - storage of finished products in warehouses, when you can already get money.
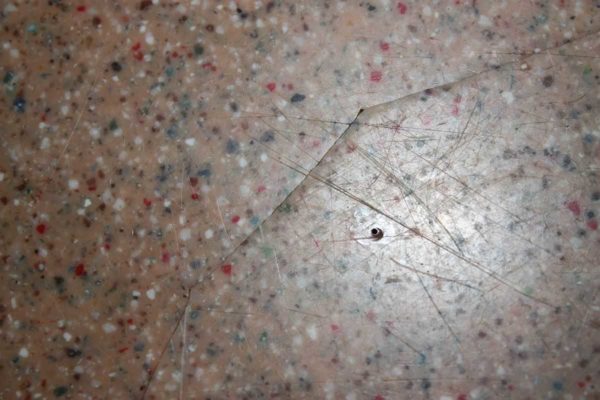
And this is the look after several months of use. And not to say that the use is "in hard mode". An ordinary family
This option is the most inexpensive, attractive in appearance, but also the most unreliable. Within a month, scratches appear, which greatly spoil the appearance and mood of the owners.
Agglomerate
This is stone chips and a little binder (4-6%). Most of the stone chips (ideally 96%) are hard quartz or granite. Polyester is used as a binder. Various natural and not so stones / substances can be added to the composition "for color and variety". It can be marble chips, colored glass, glitter, etc.
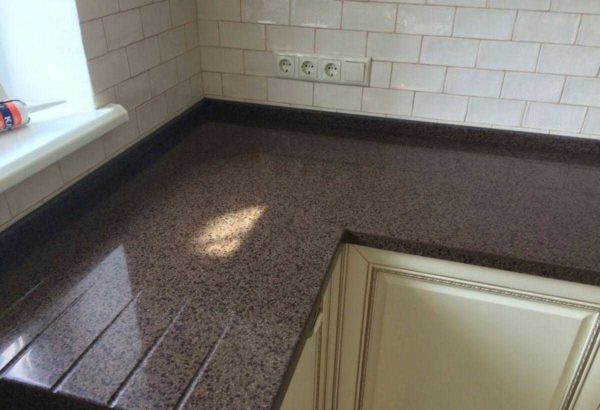
Externally, the agglomerate cannot be distinguished from acrylic, but in terms of performance, they can vary greatly
Quartz or granite agglomerate is much stronger. In fact, it is a stone with a slight addition of plastic. It is resistant to mechanical stress. You can scratch, but you will have to make a solid effort. If scratches do appear, they can be polished. This process is long and tedious. But the tabletop looks great for a long time.
Acrylic sellers say that quartz and granite "fade". It's true. Many natural stones - such as marble, quartz, granite - have a certain natural background radiation. But the main thing here is natural. It is not harmful and cannot affect health in such doses. The second "minus" that is attributed to natural stones is their fragility. Well yes. They shatter if you hit them very hard. But the action must be applied pointwise and of such force that it is simply impossible to create it in the kitchen. In general, if possible, it is better to choose an agglomerate for the countertop.
Sheet artificial stone
This technology is used if a worktop of considerable thickness is needed. The same agglomerate of great thickness is very heavy and expensive. And there is no sense in using an array. One-piece agglomerate is made with a thickness of no more than 2-3 cm. If you need a thicker slab on kitchen cabinets, it is cheaper to veneer the base.
On the base - moisture resistant MDF, chipboard or plywood (plywood is the best option) - a layer of "stone" is glued. The plane and ends are glued. A special super-strong and fast-hardening glue is used. The glue is tinted to match the coated. After hardening, the seams, joints, drops are sanded. When done well, these countertops are very durable and practical.
The sheet "stone" is different. It can be one of the types of acrylic or agglomerate. With the agglomerate, everything is clear. It's really durable and reliable. It's just that in this case more expensive varieties are often used, for example, with marble. Acrylic sheet is a cheaper option. Despite the fact that it is plastic, in terms of performance, it is better than its injection molded counterpart.
Builds to say that the agglomerate can be "not very". If a crumbling aggregate is used in it, if the binder is of insufficient quality, there will be scratches, stains, and chips. If you decide to order from a company, it is better to find those who are already using their products. And ask about guarantees. But keep in mind that in our reality, often one legal entity is closed, another is opened. And that's all. All guarantees from the legal entity have burned out. More reliable in this respect guarantees from a private trader.
Which technology is easier to master on your own
If we talk about self-production, then the easiest way is to make a tabletop from cast acrylic. True, if you use ready-made mixtures, the price will turn out to be almost the same as when ordering from a company. The next most difficult process of making a tabletop is from agglomerate. Since there is little binder, it is not easy to achieve a smooth finish. If you are not afraid of long-term grinding to obtain a normal result, you can try to master this technology.An agglomerate-based artificial stone countertop is the best choice in terms of durability and appearance.
The last "in lightness" technology for the manufacture of countertops is from sheet stone. A lot of precise trimming, gluing of parts and grinding. You need professional tools - a circular saw with guides, a jigsaw, a circular sander with a set of polishing discs. It also takes a lot of clamps to attract and fix the glued fragments.
Do-it-yourself cast acrylic table top
It seems to many that a one-piece worktop without seams is the best possible option. Easier to clean, there can be no leaks. This is true, but the material itself (acrylic) is not always good for use. Acrylic itself is a great material. For a bathroom, an artificial stone countertop is a good choice. There are very few opportunities to scratch the surface, no high temperatures. And moisture, steam, soap and other detergents are not afraid of plastic. If you decide to master the technology of casting acrylic countertops, you can try to make it for the bathroom.
Preparation
A mold is made for pouring acrylic. For its manufacture, use laminated chipboard or MDF. If the surface of the countertop is to be smooth, the formwork material must also be smooth. If you need texture, it should be on the form. Once removed from the mold, the acrylic stone will repeat all the notches and bumps. Therefore, we are scrupulous in the selection of material for the form.
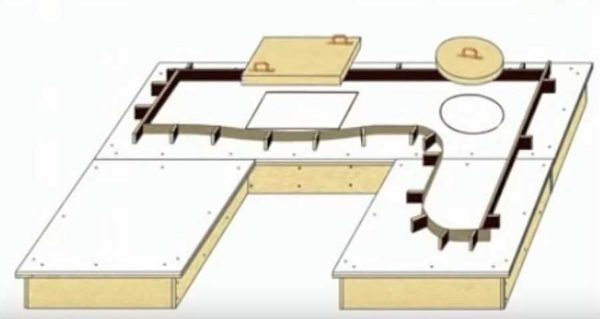
We frame the cut out workpiece with sides, close the holes for the hob and sink with technological plugs
Bumpers are made of the same material. The edges of the planks are sanded first with a coarser cloth, then with an increasingly thin emery disc. Increasingly decreasing grit is used. Remember that all defects will then be cast in acrylic. And they are very noticeable if the stone was chosen in a single color, without inclusions. The seams are sealed and leveled. The structure is thoroughly cleaned, dried, then waxed from the inside.
Countertop manufacturing
Fillers are added to acrylic - stone or marble chips, pigment, decorative components. Everything gets mixed up. The hardener is poured last. Acrylic is poured in several layers, therefore, the hardener is added only to part of the composition.
Acrylic composition is poured into the finished formwork. Distribute it evenly over all areas. It should spread over all form elements. In this case, the appearance of bubbles must not be allowed - the air must be removed. After the composition has been distributed, a chipboard sheet is laid on top, which is also greased with wax. Load is placed on the chipboard. It must be selected carefully so that the composition does not squeeze out on the sides. The cargo is left for half an hour. Then they take it off, raise the chipboard. A second portion of plastic is poured into the mold and left for a day. During this time, the acrylic will harden. Formwork can be removed.
Installation on the frame and polishing
After the plastic plate has been removed from the formwork, it is attached to the frame. Acrylic is an elastic material. Even with a thickness of 20-30 mm, it bends. The frame is assembled to ensure dimensional stability. It is made of wood (beams 50 mm thick or more) or moisture-resistant plywood (27 mm thick). The frame consists of strips along the front and rear pillars, transverse jumpers installed in increments of 40-50 cm. The strips are also placed in places of support on the furniture frame. We need more reinforcements in places of greatest load. This is where the hob or sink will be installed.
The frame is made with acrylic thickness more than 10 mm. A thinner layer requires a solid base.That is, from the same plywood you need to cut out a repetition of your countertop and glue these two sheets together. The thickness of the plywood is 27 mm or so. You can glue two thinner sheets together. It turns out cheaper. For normal gluing, the sheets are fixed with clamps.
Final finishing - grinding. First, with fine-grain discs - 320 and above, and finally - with a polishing attachment. This stage is important for appearance. Most of the flaws can be removed. But you can do harm.
Sheet stone
It would seem that it is not a problem to do something from sheet plastic or, as it is called, artificial stone. That's how it is. Parts of the desired shape and size are cut from the sheet, they are glued together. The seams are polished, removing at the same time possible differences in height.
The assembled structure is either glued to a solid base (with a stone thickness of up to 10 mm), or a frame is made of wood or plywood. Everything seems to be simple. Except that:
- A sheet of material weighs a lot, turning it over is still a pleasure.
- The cuts must be perfect, the fit of the parts must be perfect. This requires professional equipment and the ability to handle it.
- The joints are glued and fixed with clamps. They are placed approximately every 20-30 cm. Even for gradual unhurried work, the number of clamps is about ten.
- A good sander is needed to sand the joints. You can do with grinding discs for a grinder. But at the same time, the tool must be with the ability to adjust the speed.
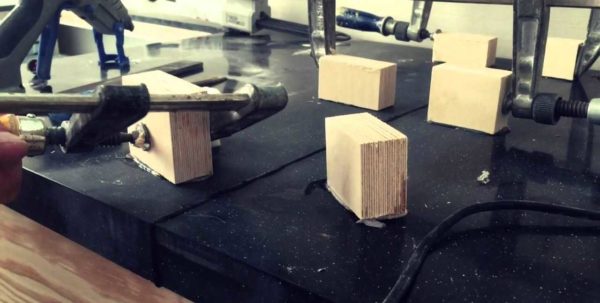
In order to pull the parts of the tabletop as tightly as possible, they put temporary stops. Clamps cling to these stops
And so yes. You can make a countertop from sheet artificial stone with your own hands. To have an idea of how and what it is about, watch the video. There are practically no explanations, but the work technology can be traced. But for a better connection of parts (when gluing an edge), it is better to choose a quarter in the main sheet. So the seam will not be so noticeable, and the connection is more reliable.