How to make scaffolding
During the construction, repair and maintenance of a private house or cottage, some work has to be done at a height. Not everything can be done with the help of a ladder, and it is not very convenient. It is much more convenient to use scaffolding.
The content of the article
Homemade wood scaffolding
Metal scaffolding, of course, is reliable and durable, but most often they are made of wood. Anyone can work with wood, and all that is needed is a saw, nails / screws, a hammer / screwdriver / screwdriver. The set of tools is uncomplicated, which any owner can find, and if there is not something for the purchase, a lot of funds are not required. Metal is more difficult in this regard. It requires at least some handling skill, a welding machine and at least some idea of how weld seams correctly... That is why do-it-yourself scaffolding in most cases is made of wood.
What to make
Everyone understands that scaffolding or scaffolding is needed for a short time. But it is necessary to use good quality construction wood for their manufacture, with a minimum of knots. Some craftsmen advise making forests exclusively from spruce. Unlike pine, its knots are located singly and have almost no effect on the strength of the board.
But spruce boards are rarely available, but pine is usually enough. It is also possible to make scaffolding from pine boards, but each of them must be checked (in any case, which go to the racks and flooring). For this, two columns are stacked (three or four bricks one on top of the other, a couple of building blocks, two boulders, etc.). When checking three-meter boards, the distance between them is 2.2-2.5 m. A board is placed on the posts, standing in the middle of it, they jump a couple of times. If there are weak points, the board will break or crack. Withstood - can be used.
It is necessary to speak specifically about the thickness of the board, being tied to the construction of the scaffolding, the distances between the racks and the planned load. The only thing that can be said is that for racks and flooring, a board with a thickness of 40 mm or 50 mm is most often used, for jibs - 25-30 mm. Such a board can be used in the most detailed construction work, if it is possible not to damage it when dismantling the scaffolding.
Nails or screws
The dispute about whether nails or screws are better always goes on, but in this case it is aggravated by the fact that the work is carried out at a height, and increased reliability is required from the structure. From this point of view, nails are better. They are made of soft metal and when loaded, they bend, but do not break. Self-tapping screws are made of hardened steel, but it is brittle and break in the presence of shock or alternating loads. This is critical for scaffolding - there were cases when they fell apart. But this is about the "black" screws. If still anodized - yellowish-green - they are not so fragile and can easily withstand all loads. If you are seriously worried about the reliability of the scaffolding, it is better to use nails. They are not liked due to the fact that it will not be possible to disassemble the connection quickly and without loss - most often the wood is damaged.
When making scaffolding yourself, you can do the following: initially collect everything on anodized self-tapping screws. If the design turns out to be convenient and correct, insure yourself by driving two or three nails into each joint.In order not to damage the wood during disassembly, you can put scraps of thin boards under the nails; whole boards, but of small thickness, can be used on an extended span. When disassembled, it can be split, and protruding nails can be easily removed.
Designs and their features
For different types of work, scaffolding and scaffolding of different design are used. For work with light materials, too much load-bearing capacity is not required. In such cases, an additional scaffold or an envelope scaffold is made.
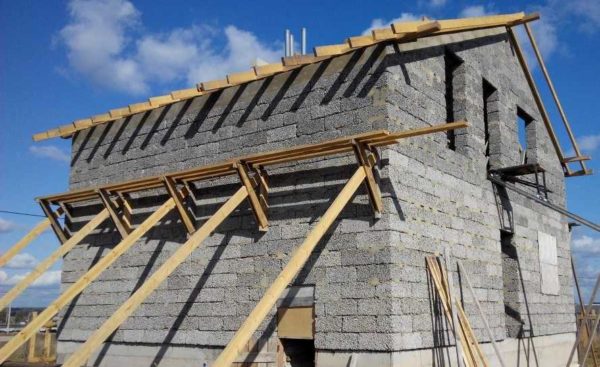
Building scaffolding envelope. Despite the seeming unreliability, it is convenient to work with them
For work on the gables or for the exterior decoration of a low one-story house, construction goats are used, on the crossbars of which the flooring is laid.
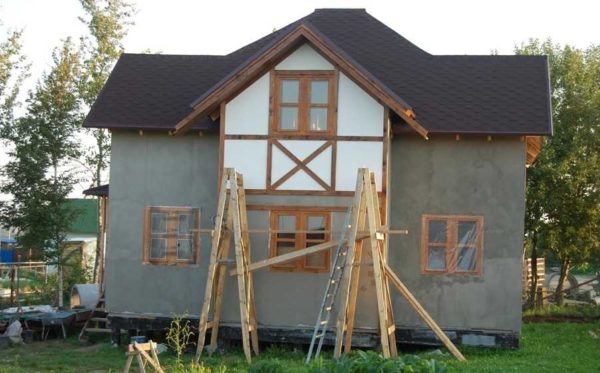
If nothing can be supported on the walls, construction trestles with floorboards laid on the crossbars are suitable
For laying brick walls, any building blocks, for finishing the facade with bricks or stones - all these works require full-fledged scaffolding.
As a rule, all these structures are not attached to the walls of the building, but are fixed with stops that support the racks. Let's take a closer look at each of these designs.
Additional scaffolds
They are called so due to the fact that they are usually not attached to the wall, but simply lean against the wall. They are held by the support. The more this type of scaffolding is loaded, the more durable they stand. There are two designs, both of them are made in the form of the letter "G", only deployed in different directions.
The figure on the right shows a simple and reliable scaffold design. Their only drawback is that they are not height adjustable. Convenient if you need, for example, to hem the roof overhangs, to mount or clean the drain, all those works that have a small variation in height. Some even adapt such a scaffold for building a log house (bar). It is convenient to roll or lift logs along the edges of the stops.
- They are reliable - they can withstand an 11 meter log and three people
- Scaffolding - simple construction
In the picture on the left, an envelope scaffold or Armenian scaffolding. The design is simple and reliable, although it does not seem so. But it has already been tested on many thousands of houses under construction. It is attractive because it requires a minimum of building materials; you can assemble / disassemble / move them in a matter of minutes. The main thing is to make triangles, and setting it to a given height takes a little time: raise the triangle, support it with an inclined beam, which is fixed in the ground.
For the manufacture of triangles, a board 40-50 mm thick, 100-150 mm wide is used. The vertical part can be long - for it it is convenient to raise the platform to a given height. The upper crossbar is made 80-100 cm long, flooring boards are laid on it. By the way, they are also 50 mm thick, and the wider the better, ideally also 150 mm.
When making corners, the joint must be positioned so that the horizontal board is on top. To increase the reliability of this unit, you can use metal plates in the form of a corner. But if the corner is fixed with the help of three jibs nailed on both sides, this is not necessary.
Such triangles are installed approximately every meter. If the facade allows, they are nailed, if not, they are dispensed with only by gravity. The main load in this structure falls on a thrust board - the one that is set at an angle and rests against the ground at one end, and at the top of the triangle with the other. These stops are made of timber, boards with a thickness of at least 50 mm, pipes of a solid diameter (at least 76 mm) or section (for a profiled pipe at least 50 * 40 mm).When installing the stop, it is placed exactly in the corner, hammered into the ground, and additionally fixed by driving in wedges.
To exclude the possibility of lateral shift, the installed stops are fixed with several jibs connecting them into a rigid structure. For these jibs, you can use an unedged board, if there is one, but of sufficient thickness and width.
If it becomes necessary to grow stubborn boards (if they are needed longer than 6 meters), an additional emphasis is made for such a board. It rests approximately in the middle of the main one, taking off part of the load.
Now a little about the flooring of these attached scaffolding. It is made from a wide board 40-50 mm thick. In this case, it is desirable to fix them to the triangles at least with screws. This design does not provide for the presence of a railing, and the slightest movement under the feet will cause increased discomfort. Therefore, fixation is highly desirable.
Wooden scaffolding: drawings and photos
The above options are good if the job does not involve heavy materials. Also, it is not always possible to support the scaffolding on the wall - any ventilation facade or multilayer wall - and you will not be able to install such a structure. In this case, full-fledged forests are made. Their design is also not complicated, but a decent amount of lumber is required.
For their device, boards of considerable thickness are also used - 40-50 mm. Racks are assembled first. These are two vertical beams or thick boards held together by crossbars. The dimensions of the crossbars are 80-100 cm. They should be made on the basis that the minimum, more or less comfortable flooring width is 60 cm. But you will feel much more confident if you have at least 80 cm. To give the structure more lateral stability racks can be made tapering upwards.
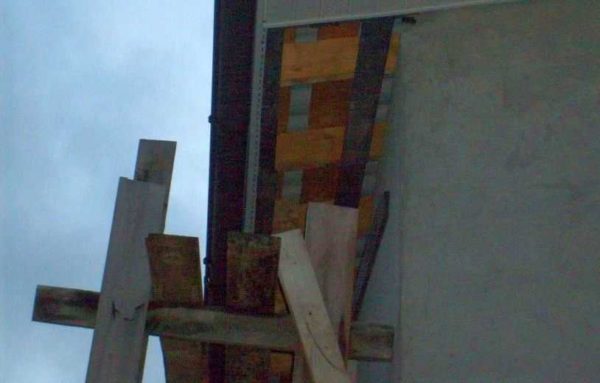
To prevent the scaffolding from collapsing on the wall of the house, the crossbars can be made with a release of 20-30 cm.They will not allow the structure to fall towards the house
Racks are placed at a distance of 1.5-2.5 meters. The span depends on the thickness of the boards that you will use for flooring - it is necessary that they do not bend. The racks installed at the required distance are fastened together with slopes. They will not allow the structure to fold sideways. The more crossbars and jibs, the more reliable the scaffolding is.
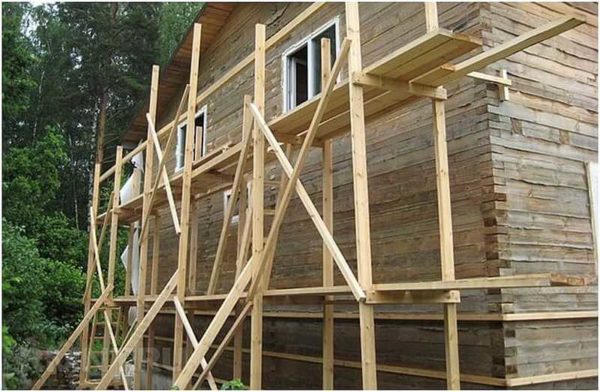
To prevent the scaffolding from falling, they are propped up with boards / beams, one end of which is nailed to the racks (with nails), the other is buried in the ground
The cross beams prevent sideways folding, but there is still the possibility that loose scaffolding could fall forward. To prevent this from happening, the beams are supported with jibs. If the height of the scaffolding is 2.5-3 meters, you do not need to do this, but if you need to carry out work at the level of the second or third floor, such fixation is necessary.
If the work will be carried out at a high altitude, it is advisable to make a railing. They can be made from a not very thick board, but there should be no knots, as well as cracks. The handrails will help those who are afraid of heights to feel more confident at the top.
- The construction of the scaffolding is modular, can be easily extended to the required height and shape
- Up to the overlap level of the second floor there is enough standard molding - 6 meters
- Such scaffolds are inconvenient in that they have to be completely disassembled if it becomes necessary to move them to another wall
- It is possible to assemble small scaffolding from old but sturdy boards. Sometimes poles or pipes are used for braces and stops - what is on the farm
Construction goats
There is also a way to make lightweight mobile scaffolding - to build the same construction girders, stuffing with a certain pitch crossbars, which will be both a ladder and a support for the floorboards.
This version of scaffolding is good, for example, when sheathing a house with siding. The cladding goes from bottom to top, the height has to be changed all the time, there is no way to lean or fix against the wall. Therefore, this option is the best for such a case.
Sometimes one rack on one side is made vertical, without inclination. This allows them to be installed closer to the wall, the flooring is then located closer to the wall. In some cases this is convenient - for example, when caulking, painting, preventive treatment.
Types and units of metal scaffolding
When building a house from stone, building blocks, metal scaffolding is more suitable. They are able to withstand any load. They are less popular only because in many regions wood is still the cheapest type of building materials. The second point, which is often decisive, is that after dismantling the wooden scaffolding, the boards can be put into action - used in further construction. And parts of the metal should collect dust in barn.
But metal scaffolding also has its advantages. When disassembled, they do not take up much space. The owners of wooden houses still have to use them periodically: a log house requires maintenance, so once every two or three years, forests are needed. It is more practical in this case to be made of metal rather than wooden. They are easier to assemble, more durable and stronger.
All metal scaffolding has the same shape - vertical posts connected by crossbeams and slopes. Only the way the parts are fastened to each other differs:
- Pin scaffolding. They are called so due to the fact that the crossbars with the posts are connected with pins. Pipe sections or perforated discs are welded on the racks, and bent pins are welded on the crossbars. Such a system is assembled very simply, it can withstand heavy loads. It is very simple to implement pin scaffolding for buildings of a simple form, bypassing bay windows and ledges is much more complicated.
- Clamp. For racks and crossbeams, circular pipes are used, which are fastened together using clamps of a special design. The system turns out to be very mobile and mobile, you can easily bypass any curved facades. Minus - limited carrying capacity and height (according to GOST - no higher than 40 meters).
- Framed. Frames of the same size are welded from a round or rectangular pipe. They are connected to each other by transverse pipes and jibs. They have a modular structure, can be easily extended both in height and in length. They have a certain step in length - 1.5 / 2 / 2.5 / 3 meters, one section is usually 2 meters high in height, the standard depth is 1 m. Some frames have wheels - for easier movement on a flat surface. Connection of flag-type elements - pins with a slot are welded on the frame, into which the flag is inserted. Holes are made in the crossbars and slopes. The elements are put on a pin, fixed with a flag. The sections are extended upward using connecting pipes of a smaller diameter, welded to the frame posts on one side. With this method, ideally matched pipe sizes are important so that there is no backlash.
- Wedge. With a general similarity, the designs differ in the form of the connection. On jays with a certain pitch (usually 2 meters), perforated discs are welded. On the lintels, at both ends, special wolf's mouth locks are welded. The locks are fixed to the disc using a specially shaped wedge.Such scaffolds are connected and disconnected quickly, have high mobility, and can be used on facades of complex shapes.
When self-manufacturing metal scaffolding, pin-type ones are most often made. They are the easiest to implement, however, they are good only on rectangular facades, to bypass more complex shapes, you have to cook additional pipes.
Clamps are an important component of metal scaffolding used in construction, installation and repair work. Depending on the design, there are rotary and non-rotary clamps. Also, products differ in the production method. Clamps on the market today are manufactured using a forged or stamped method. To prevent rust, the products are treated with a layer of zinc.
The standard clamp is a clamping bracket with a screw that can securely fix iron pipes. The design of the product has been carried out in such a way as to successfully resist the multidirectional loads that appear when working on scaffolding. The clamps can be used multiple times.