How to make a wood splitter
Harvesting firewood requires significant effort: they need to be sawn, chopped, folded into woodcutter to dry. Most of the energy is spent on chopping firewood. A wood splitter can facilitate and speed up the process. They are presented in sufficient quantities, but they cost a lot of money. At the same time, you can make the simplest wood splitter with your own hands from scrap metal - pipes, corners, etc. Everything will take literally several thousand - if there is no metal, you will have to buy it.
The content of the article
Mechanical wood splitters
If the volumes of firewood are small, a mechanical wood splitter can easily handle them. They differ in simplicity of design, the minimum number of complex units, and also in that the costs are minimal, even if there are no suitable pieces of iron on the farm.
Simple do-it-yourself wood splitter: mechanics
The simplest mechanical wood splitter resembles a well crane. The design is one to one, only a cutter and handles are fixed instead of a bucket. The connection of the rack (racks) and the crossbeam can be made the simplest - articulated. Only good lubrication is required.
The principle of operation is probably clear to everyone. The block is placed on a support, the lever is pulled down sharply, due to the force of inertia, the chisel gains significant force and splits the block. The process is repeated until logs of the required thickness are obtained.
It's easy to assemble such a mechanical wood splitter with your own hands, and, literally, from what is - pipes, a corner of any size, you can even use an ax as a cutter. In addition, such a structure can be made collapsible so that it can be carried.
There are a lot of cons. Chopping wood requires considerable effort. Moreover, more efforts are made to stop the cleaver's course after the log has fallen apart. The second minus - such a log splitter occupies a solid area, because the longer the lever, the less effort you need to apply. Nevertheless, even such a primitive mechanical device greatly reduces the complexity of the process.
In this design, the cleaver must be heavy. Therefore, the blade itself is welded to an all-metal blank. A more affordable option is to weld it to a pipe (round or square) and fill it with concrete. Agree, making such a wood splitter with your own hands is within the power of anyone who knows how to handle welding machine.
Spring log splitter
There is a modified design of a manual mechanical wood splitter, which, with a smaller size, splits firewood better, requires less effort. In this model, the main working unit is a spring, which is fixed on the bed, and its upper part rests against a stationary crossbar, on which the cleaver is fixed.
In this design, the main effort - to hold the cleaver after the log has split - is taken over by the spring. Accordingly, the main thing is to choose a spring and an emphasis so that minimal efforts are applied, but they were sufficient to split even complex, knotty block of wood. The spring support can be made movable. Then you can adjust the parameters for specific conditions. In reality, "readjustment" is required for a specific person. If one person will work with the tool, then everything can be done stationary, choosing the height empirically.
It is equally important to make a movable joint between the frame and the lever, on which the cleaver is fixed. The best option is bearings. They must be of high quality, preferably self-leveling.
The minimum height of a homemade wood splitter is about 800 mm. But then you either have to work by bending over, or install the machine on the table / bed. A more comfortable option that requires minimal effort is made to fit your height. Determine at what height it is convenient for you to stand the log, to this figure you add the height of the block itself, you get the height of the bed. In this case, you will also have to bend over, but only when you set the chock on the stand, and not every time the cleaver is lowered.
- A ready-made homemade wood splitter with a spring with the specified dimensions
- The crossbar carries a large load, therefore it is not superfluous to strengthen it, it is also good to strengthen the platform for the spring
- Spring and cleaver for wood splitter
- You can work with one hand or come up with a clamp for setting logs (more secure)
- Diagram of a spring wood splitter for self-production
- The base is made in the form of a triangle. This is a stationary option
- Joint assembly and spring attachment - several options
To add mobility structures, the frame is welded, on one side of which the wheels are fixed, on the second, stops are welded. Making such a wood splitter with your own hands is somewhat more difficult, but if there is a spring and bearings, this is such a difficult task.
Inertial vertical log splitter
Another simple option for self-production. To make such a wood splitter with your own hands, you need two pipes of a larger and smaller diameter. You will also need a heavy plate - a base, and, in fact, the piercing part - a cutter / cleaver.
The design is one of the simplest, little effort is required. A thick-walled pipe is fixed on a massive platform, or better - a pin. Height - about a meter. This is the leading pipe. A cleaver moves freely along it, which is welded to the rings of a pipe with a slightly larger diameter than the leading pipe. He chops wood in the following way: lift up the cleaver and release it. You can accelerate down a little. Due to the force of gravity, the log splits.
- A heavy cleaver is the key to success in this model
- Mechanical log splitter vertical: drawing with dimensions
- To increase efficiency, you can make a weighting agent
But this mechanical wood splitter does not immediately split all block of wood. To increase its effectiveness, a weighting agent can be made on the cleaver. It can be "added" as needed. The second option is to hit the column with a hammer a couple of times. This method is good if the cutter is stuck in the wood. An alternative is to raise it together with the block up and sharply lower it. But it's easier to swing a hammer.
Electric wood splitters
A manual wood splitter, of course, makes it easier to harvest firewood, but it still requires solid physical effort. Not so much as they are spent waving with an ordinary cleaver, but still ... The electric motor helps to make the efforts even less. On its basis, wood splitters of various designs are made. But making such a wood splitter with your own hands is more difficult. Here, the device is more complex, and at least minimal knowledge of electricians is required - desirable connect the motor through the starter, and with the buttons "start" and "start".
Screw (conical)
One of the most common models is a cone or screw log splitter. The only difference between them is the absence / presence of threads on the piercing element, which in this model is made in the form of a cone.
Churbaks split due to the fact that the cone rotated by the motor cuts into the wood, gradually tearing it apart. In large logs, the edges are first chipped off, then the middle is torn apart.
Taper and thread options
First, the cutting part was turned into a smooth cone. If you use a smooth cone, you have to lean on the block quite hard during work so that the cylinder "bites" into the wood. The process is much easier if a thread is cut on its surface. In this case, the block is somehow screwed onto the screw, and then cracks.
The main thing is to correctly make a threaded cone. If you have a lathe and work experience, you can try to do it yourself. If not, you will have to order. The thread is made different, but the following parameters are recognized as optimal: a step of 7 mm, a depth of 3 mm (minimum - 2 mm). Another important point is that the depth of the seat on the motor gearbox is at least 70 mm.
If there is a threaded cone, making this wood splitter with your own hands will not be difficult.
Electric motor and gearbox
You need an electric motor powerful enough (2 kW or more or 5-9 l / s), but with a low speed: 250-600 rpm. At 250 rpm and below, it splits very slowly, and if the rpm is more than 500, it is dangerous to work, as it can pull the log out of the hands.
If you manage to find an engine with such parameters, you can put the made lance (screw) directly on the crankshaft (pictured above). If there are more revolutions, it is necessary to install a reduction gear or make a chain or belt drive to reduce the speed.
The ratio is calculated depending on the engine speed. For example, there is a 900 rpm engine. Having made a 1: 2 gearbox, we get 450 rpm. Just the best option.
Transmissions can be belt or chain. Chains work many times louder, require constant strokes, and it is usually more expensive to carve sprockets with the necessary parameters. Double belt drive is desirable (as in the photo above). In this case, there will be less slippage.
- Homemade screw log splitter with an electric motor
- Chain drive is noisier but more reliable
- Insecure construction. It is advisable to cover both the chain and the motor with a casing
- An emphasis is needed to hold the chain in tension
- Emphasis on the other side
- This is approximately the thread cut on the cylinder for the wood splitter
- "Extension" for the screw - to keep the work area away from the motor or belts / chains
Where to place the motor
If the design provides for the presence of a transmission, it is better to put the motor below, and fix the screw itself on the working surface. Choose the height of the working surface for your height so that you do not have to work in an incline.
There is also such a parameter as the height of the screw above the working surface. The gap from the table to the cylinder should be in the region of 8-20 cm. It should not be placed higher - it can turn small-diameter blocks of wood. The optimal distance is 8-12 cm. Even small blocks of wood do not turn.
Hydraulic wood splitter
The hydraulic log splitter is the most powerful, but also the most difficult and expensive to manufacture. In addition to the bed, engine and cutting knives, a hydraulic cylinder with sufficient power is required. They are not cheap. In addition, an oil tank and a pump are needed.
A hydraulic splitter for firewood develops solid efforts, therefore, in its manufacture, metal of considerable thickness is used - 6-10 mm, depending on the drive power. The developed effort is quite enough to break the chock into 6-8 logs at a time. Therefore, knives are made in the form of an "asterisk".
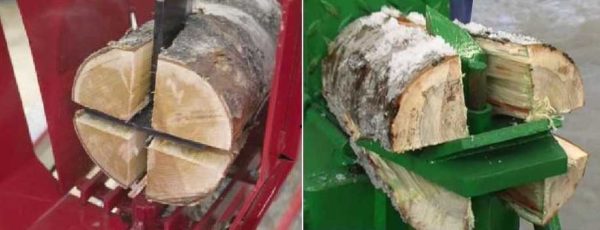
A hydraulically driven cleaver is equipped with a complex cutter, which breaks the block into several logs at once
When knives are made, they are spaced a few centimeters apart. So that there is only one in the work.For example, first - horizontal, then - vertical, then - right and finally - left. In this case, reinforce each of the knives by welding reinforcing plates on the back. It is advisable to use hard steel, having previously sharpened it according to the same principle as on cleavers.
Related Videos
The petrol wood splitter works quite fast, though the hemp is birch. I had to chop an elm with a cleaver - this is a real hassle, the cleaver gets stuck in the wood. Judging by the video, a gasoline wood splitter should also handle an elm tree.
Now, when chopping an elm tree, you understand that it is better to mechanize the process. In general, with an elm and a hand cleaver, I used the following algorithm - first I chopped off the edges of the chock, and only then chopped the middle. There is no other way, the cleaver simply gets stuck in the hemp.
Business is moving towards winter and people are talking about wood splitters 🙂 Only today I found out that there are factory Gorynych and there are already a lot of reviews on this unit - one feast for the eyes is working. I liked it, decided to look at the prices and was taken aback - it costs from 100 thousand rubles !!! However! The purchase is canceled and you have to think again how to make your own.
I fired up to do it, read it, the fuse was gone ... I'm going to chop it with an ax and a sledgehammer ... Who's got firewood today?