Fusion roof
Modern welded roofing has a service life of up to 25-30 years - the current materials retain their properties precisely during such a period of time. But this is provided that each of the layers is correctly installed. Errors are unacceptable, since there is no way to fix them. We'll have to dismantle a piece of the roof if the errors are local or all if they are global. Probably for this reason, many homeowners prefer to make a welded roof on their own - a self-made roofing, as a rule, costs longer without leaks.
The content of the article
The structure of materials for the welded roof
The materials for the overlaid roof have a multi-layer structure. An astringent is applied to the base on both sides, and a protective coating is applied to it. All of these layers have several options. Their combinations give different properties and characteristics.
Base types
A significant part of the properties of the material is determined by the base on which the binder is applied. If it can stretch, then the material for the deposited roof can also change its size to a certain extent, if it does not tolerate deformations, then the material also breaks. There are the following basics for hardfacing:
- Roofing cardboard. A fairly strong and inexpensive base, popular due to its low price. All types of roofing material are made on the basis of roofing cardboard. Therefore, when marking in the first position, put the letter "P", which denotes this material. This is a good choice for temporary roofing - the service life of roofing material is up to 5 years. But the scope of application of roofing material is rather limited - it begins to burst and crumble at temperatures above + 40 ° C and less than -20 ° C. And this is its main disadvantage.
- Asbestos paper. On this basis, Hydroizol is made. It is mainly used in the underlayment of roofing cake as a waterproofing layer. It has a low price, but its service life is up to 5 years.
- Glass-bed. Strong base that is not easy to break. When the roof moves, materials based on fiberglass can come off the surface, but rarely break. It is marked with the letter "C" (in the first position of the designation).
- Fiberglass. Non-woven fabric, of medium strength, suitable for stable substrates where movement is unlikely. Fiberglass in the marking is indicated by the letter "X".
- Polyester, durable and stretchy fabric. Polyester weldable materials can stretch up to 30% of their original size without compromising integrity. It is designated by the letter "E" at the first position in the designation.
The most durable materials are made from polyester. Manufacturers say that these materials retain their properties for 25-30 years. This is how many weld-on roofs can be used without repair, however, with proper installation. The disadvantage of polyester-based surfacing materials is the high price at the time of installation. But you can save on repair and replacement.
Binder types
The binder also determines the set of properties of the material for the welded roof, but it no longer affects the strength, but the waterproofing properties and resistance to weathering.Also, this layer is responsible for the degree of adhesion (adhesion) to the base or the underlying layer. There are the following types of binders:
- Bituminous.
- Based on tar.
- Bituminous tar.
- Rubber-bituminous.
- Rubber-polymer.
- Polymeric.
The best characteristics are for rubber-bitumen and bitumen-polymer compositions. They have a wide range of temperatures at which they can be used. When selecting materials for a welded roof, be sure to pay attention to this parameter, because some of them tolerate high temperatures well (up to + 150 °), and some - low ones (up to -50 ° C). And you cannot confuse them in any way.
Appointment
The cladded roof is usually multi-layer, and the materials for different layers must have different characteristics. Those below must provide waterproofing, sound absorption, and, if possible, have thermal insulation properties. These materials are called lining and when marking it is indicated by the letter "P" in the third position in the marking.
The deposited materials for the upper layer of the roof must additionally have a high surface resistance to mechanical damage and weathering. These materials are called "roofing" and in the abbreviation are designated by the letter "K" in the third position.
Protective layers
Since the binder in the materials being welded is sticky, it must be covered with something. This is done using stone chips of various sizes or plastic wrap. Sometimes foil (Folgoizol) is used as a protective layer. Such materials are used in countries with hot climates. Foil is needed to lower the temperature - the lower layers heat up 15-20 ° C less than when using conventional materials.
Stone chips (dressing) are:
- Dusty (P) and fine-grained (M). Used to prevent the layers from sticking together in a roll.
- Coarse-grained (K) or scaly-mica (Ch). It is used on roofing materials from the front side to protect against mechanical stress and weather protection. In addition to these tasks, it also performs decorative functions - the crumb is painted in different colors.
Since the type of protective coating has a significant impact on the characteristics and scope of materials (fine-grained and dusty on both sides are applied to the lining materials), their designation is also in the marking - this is the second letter.
These are, in short, all the characteristics that you need to know when choosing a weld material. Before purchasing, be sure to read the description, study the scope and specifications.
The technology for laying a soft roof without fusing is described here.
Base requirements
The welded roll roof is most often made on a reinforced concrete base, the joints between the slabs must be sealed with a mortar of grade M150 and higher. Also, the grounds can be:
- Rigid mineral wool slabs (tensile strength not less than 0.06 MPa. If the roof is melted directly on them, the surface is preliminarily treated with hot roofing mastic with a consumption of not less than 1.5 kg / m2.
- Thermal insulation made of monolithic lightweight concrete with fillers such as perlite, vermiculite. A screed made of cement-sand mortar, grade of at least M150.
- Extruded polystyrene foam.
- Asphalt base, compressive strength not less than 0.8 MPa.
- Prefabricated screeds from flat asbestos-cement and glass-magnesium sheets, DSP (cement-bonded particle boards). The minimum thickness of the slabs is 8 mm, they are laid in 2 layers with a gap in the joints. One seam from another is spaced at least 50 cm apart. Fastening of layers to each other - in the center and along the perimeter, fastening type - riveted, it is possible to use self-tapping screws.When fastening to self-tapping screws, it is necessary to pre-drill holes, the diameter of which is 1-2 mm less than the diameter of the fastener. At least 14 fasteners are installed on one sheet of 300 * 150 cm.
- Backfill of perlite and expanded clay, on top of which a cement-sand screed with a thickness of at least 50 mm is arranged. The screed must be reinforced with a road metal mesh.
If the roof is flat, it is necessary to form a slope towards the drain or drainage funnels of at least 1.7%. This is usually done with insulation. Manufacturers of roll deposited materials produce insulation boards with a given slope. They are simply laid, observing the direction.
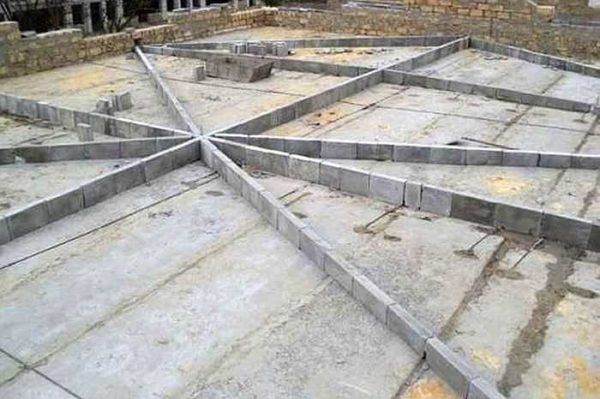
Another way to form a slope is to set the guides before pouring the screed and level the concrete along them
You can find a bituminous shingle roofing device here.
Roofing cake composition
When installing a pitched or flat surfaced roof, the cake is the same - with or without insulation, but it necessarily has a vapor barrier layer. The material for the vapor barrier is selected for the roofing used, as well as the underlay carpet is chosen for it.
It's all about the compatibility of qualities and characteristics, therefore it is advisable to use all the elements of one manufacturer on the roof. Reputable campaigns even have special tables by which you can find the desired cake. One of the most famous manufacturers in Russia is Technonikol, their table is shown below.
What's under the roofing material
The vapor barrier protects the overlying layers of the insulation from moisture saturation, which is especially important when using stone wool as a heater. She is afraid of getting wet. With an increase in humidity, its heat-insulating properties are greatly reduced, and if it freezes in a wet state, then when defrosting it will simply crumble into dust and your roof will become cold. Therefore, when laying a vapor barrier, special attention is paid to the tightness of the joints, the correct cutting of the passages.
When insulating a flat roof, you must remember the need to create a slope towards the drain or receiving funnels (at least 1.5%). The same slope is maintained when pouring the screed. Its minimum thickness is 5 cm, concrete grade - not lower than М150. The screed that has gained strength (at least 28 days from the moment of pouring) is coated with a bituminous primer, which ensures normal adhesion of the roofing cake to the screed.
On hard slabs of stone wool, fusion of materials is allowed without laying a screed. Then the surface of the insulation is coated with a primer, and the layers of the welded roof are mounted on top.
But it is not always necessary to insulate the roof. In this case, there are fewer layers (see photo).
When installing pitched skys or a prefabricated screed (from plates and sheets), the roofing cake will be the same, only the vapor barrier layer is packed from the side of the room, the insulation is laid between the logs, and the prefabricated screed sheets are attached to the logs on top (the thickness of the sheets is at least 8 mm, laying in two layers with a gap of seams).
The device of the overlaid roof
The welded roof will serve for a long time if its layers are laid according to all the rules. There are a lot of works, they are arranged in the article in order of priority.
Preparation of the base.
- All debris and dust is removed from the roof surface.
- Remove rust and other non-greasy stains with abrasives.
- Greasy stains, remove part of the mortar, leveling the formed recess with patches of cement-sand mortar.
- If the surface is relatively flat (the difference is not more than 5 mm / sq. M along the slope of the roof and 10 mm / sq. M in the transverse direction), cracks and potholes are filled with cement-sand mortar.If the floor slab is uneven, fill it with a leveling screed. For pouring, concrete of a grade not lower than M150 is used, the minimum screed thickness is 30 mm.
- Vertical surfaces should be plastered or sheathed with DSP boards, flat asbestos sheets. If they have cracks and crevices, they are sealed with a sealant or cement-sand mortar.
- Before starting the installation, treat the roof and vertical surfaces with a bituminous primer (primer compound).
In the places where roofs are adjacent to vertical surfaces, install the roofing materials to be welded to a height of at least 10-15 cm (if there are no special recommendations). In the places where the roofing surface is adjacent to the walls of the heated premises (chimney pipes and ventilation ducts, including), the approach to the vertical wall should be at least 25 cm. This is necessary so that condensation does not form in the roofing cake.
Laying the vapor barrier
Bitumen weldable vapor barrier material can be laid by fusion, or it can be laid freely, but all joints must be fused.
- The material is rolled out along the roof so that the side overlaps leave 80-100 mm, the end overlaps (the joints of two rolls in one strip) - at least 150 mm.
- End overlaps on adjacent strips must be at least 500 mm apart.
- When installing a heat-insulated weld-on roof, the vapor barrier is installed on the wall 10 cm above the thermal insulation layer.
- Places of abutment to vertical surfaces are reinforced with an additional lining layer, it is put on the hay by 250 mm and so 100 mm should lie on the roof.
Insulation layer
The thermal insulation is laid on the finished vapor barrier layer. The surface must be absolutely dry and clean. The rules are:
- The slabs are laid without a gap and fit tightly to each other. If gaps larger than 5 mm are formed, they are filled with strips of thermal insulation material.
- When laying two words, the seams are stacked apart.
- In order not to damage the laid insulation, paths are made on its surface of plate material (plywood, OSB, etc.).
- They are attached with special sharpened self-tapping screws with plastic caps instead of umbrellas.
- With the help of thermal insulation, a slope is formed towards the drain.
Screed device
A screed is poured over the insulation. When using hard slabs of mineral wool (compressive stiffness not less than 0.06 MPa), the welded roof can be made directly over the insulation, without a screed. But for greater reliability, it is better not to skip this stage. The order of work is as follows:
- A separating layer - roofing felt or glassine - is laid on mineral wool or expanded polystyrene.
- A metal mesh of wire of at least 3 mm thickness is laid with a step of 150 * 150 mm.
- Fragments of the mesh are stacked with an overlap of at least one cell (150 mm). In the overlap areas, they are tied with a knitting wire with a pitch of 300 mm.
- Guide rails are installed taking into account the formation of the slope.
- Concrete is poured between the slats. It is leveled with the rule, resting it on slats.
- Two days after pouring, the slats are removed, the resulting voids are filled with a cement-sand mortar.
The screed is left to gain strength. It takes 28 days on average. To maintain the required moisture level, immediately after installation, the screed is covered with plastic wrap, tarpaulin, burlap. During the first week, the surface is periodically moistened: at high temperatures several times a day, at low temperatures - once.
The concrete that has gained strength is treated with a primer (and the parapet too), wait until it dries (time depends on the brand and the weather).Fusion of the roofing material over the not dried primer layer is prohibited.
Adjoining vertical surfaces: installation of sides, overlaps
In the places where the roof is adjacent to vertical surfaces, to ensure tightness, it is recommended to make a side with an angle of 45 °. You can make it:
- using cement-sand mortar (grade M 150, dimensions 100 * 100 mm)
- by installing special fillets, which are produced by the same companies that produce materials for weld roofing.
Fillets are installed on bituminous mastic, the side from the solution is coated with a primer after the cement has set.
The sides are closed with an additional layer of Technoelast EPP lining carpet. A strip of such a width is cut from the roll so that at least 100 mm of material remains on the base of the roof and at least 25 mm is placed on a vertical surface. Side overlap of strips - not less than 80 mm. The material of the additional carpet laid out along the perimeter is melted on the sides along the entire width.
When laying the next layers (lining and roofing), the lining layer is also first fused, then the main carpet is laid and fused, bringing it 80 mm above the side. The width of the additional carpet strip depends on the layer.
Endova and skate
If a pitched weld roof is installed, an additional lining layer is laid on the ridge at the bend of the roof. Its width is 250 mm on each side. On complex roofs in valleys, the backing layer should be at least 500 mm on both sides of the bend.
When laying on a ridge, the joints of the canvases are placed against the direction of the prevailing winds. The overlap of the panels is at least 80 mm, the joints must be fused. In the valley, if possible, lay the underlay in a single piece. If the length of the roll is not enough, rolling starts from the bottom, moving up. The joint is also necessarily melted.
Overlay roofing: rules for laying material
First of all, you need to decide on the direction in which the rolls will be rolled. On flat roofs, this is done along the long side of the roof. On sloped roofs, the direction depends on the angle:
- less than 15 ° - rolls across the slope (along the slope);
- more than 15 ° - along the slope.
Note! Laying different layers in a perpendicular direction is not acceptable. All layers of roofing materials are laid in the same direction.
In the presence of several layers, the longitudinal seams of the layers are displaced by at least 300 mm. When laying, standard overlaps are also provided: side - 80-100 mm, end 150 mm.
Laying procedure
Begin the installation of the materials of the overlaid roof from the lowest place. Beforehand, the roll is completely unrolled, providing access to vertical surfaces (parapets, pipes, etc.). You need to roll it out without waves. So that the material does not move, when rolling, one side is pressed with something heavy (you can put an assistant). The length is marked on the laid roll, the excess is cut off.
On flat roofs, the roll is rolled from the edges to the center. For convenience, you can use an iron pipe. With a slope of more than 8%, this option does not work. In this case, fusion starts from the top, moving down. A piece 1.5-2 meters long is left uncoated. It is processed after the whole piece is glued.
So that when the rolls are rolled out there are fewer waves, a couple of days before the start of installation, they are put upside down. So they take on a round shape, the material then lies flat.
Fusing technology
Regardless of how the material is rolled, it is fused by rolling it "on itself".This way you can control the degree of heating of the bituminous layer: the whole picture is in front of your eyes. If you push the roll away from you, the quality of the roofing will be very low and the roof will leak quickly.
Burner movements are smooth and uniform. When laying, the overlap places are additionally warmed up. In this case, the burner moves along a trajectory in the form of the letter "G". The burner is positioned so that both the base of the roof and the binder on the roll surface are heated simultaneously. When properly heated, a small roll of molten bitumen forms in front of the roll.
When fusing, it is necessary to ensure that the bitumen melts evenly, there are no "cold" zones or zones of local overheating. Some manufacturers (Technonikol) apply a pattern to the underside of the materials to be welded for the roof. It is easier to control the degree of heating of the bitumen along it - as soon as the pattern "floats", you can roll out the roll and move on. If the bitumen is heated correctly, it flows out at the edges of the roll, leaving a strip of about 25 mm. That is, an even seam of dark color is obtained along the edge.
Note! It is impossible to walk on only a welded roof. The dressing is trampled into hot bitumen, which impairs its appearance and protective properties.
When laying the weld-on roof in lowered areas, the corners of the rolls at the joints are cut by 45 °. This sets the correct direction for the movement of the water.
Sometimes, when laying the finishing layer of the overlaid roof, it becomes necessary to overlay the material over the coarse-grained or flaky dressing. If you just heat the material and stick it on the sprinkle, there is a high probability of leakage. In this case, it is necessary to preheat the surface of the material with sprinkling, drown it with a spatula in bitumen. After that, it is already possible to reheat and glue.
It seems to me that a welded roof for a private house or outbuilding is not a very suitable option, it looks too official. And you won't be able to melt it yourself, and this is an additional cost. For my garage, I considered the option of a welded roof or roofing material, but as a result I abandoned this idea and made it out of Ondulin. I ordered it in an official store, brought it with my car, laid it myself and saved a lot.
With ondulin, too, not everything is as simple as it seems. Eight years ago, I covered the roof of the house with a dark green ondulin, now it is burnt out and peeled off. Apparently the color will soon turn black. I see about the same picture on neighboring houses. In short, you need to take quality material, but how can you evaluate the quality if you are not a professional builder?