How to cover the floor in a concrete garage
Having made a concrete floor in the garage, after a while you realize that the option, although not bad, is not ideal. Firstly, during cleaning, it becomes dusty, fine dust, clogs in the smallest cracks, lays down a thin light gray bloom. Secondly, the trapped liquids are absorbed, and there is no way to remove them. If the stain is oily, dirt will constantly adhere to it. After a while, the floor seems dirty all the time. So the idea comes to make a floor covering in the garage so that it does not "get dusty", it is well washed, but at the same time it is non-slip and durable.
The content of the article
Impregnations (primers, primers)
If you do not know how to cover the concrete floor in the garage so that it does not get dusty, does not get very dirty, and spend a little time at the same time, pay attention to the impregnation for concrete (also called a primer for concrete). These are multi-component formulations based on polymers. They are organic and inorganic. Since these are impregnations, they do not form any film on the surface, and therefore cannot peel off and fall behind. Their constituents penetrate into concrete, bond molecules with polymer chains. As a result, the surface strength becomes 2-3 times stronger, the resistance to aggressive environments (acidic and alkaline), temperature extremes increases, it tolerates frost better, and dust formation is also excluded.
In general, there are three types of concrete primers:
- Polyurethane. Their main purpose is waterproofing, they are also used to make a repair mortar: the primer is mixed with sand and cracks and chips are sealed with this mixture.
- Water dispersive. They do a good job of dust removal and slightly strengthen the concrete surface. Their cost is average.
- Epoxy. For the most part, they are two-component, prepared before application, the main purpose is waterproofing.
If you will not paint the floor or fill it with any other topcoat after treatment with a primer, then water-dispersion primers are best suited for dedusting the floors in the garage. For paint or other coatings, primers are taken of the same type: for polyurethane paint for concrete of the same composition, they take preparation, etc.
Polyurethane (polymer) impregnation for concrete
This garage cover is good for everyone, except for the price - 1 liter costs about $ 5. You can find packs of 3 kg and 20 kg. Impregnation consumption when applying the first layer 0.25-0.5 kg / m2, for the second - 0.15-0.2 kg / m2.
When processing, do not dilute, smear generously, at least twice. Polyurethane impregnation for concrete binds particles without forming a film. Such a concrete floor stops dusting, it will absorb less liquids. The same compounds strengthen the crumbling concrete surface. If the process has gone far, they will not help, but if only traces of abrasion are visible, impregnation will help delay the process.
Polymer impregnations are applied only to dry surfaces. The moisture content of the concrete should be no more than 5% (at least 28 days should pass from the moment of pouring). The composition is poured onto the floor in portions, spreading with a roller or a special mop over the entire surface. Some firms can add color, so at the same time you can get a colored floor in the garage. This treatment can be used as a preparation for the subsequent application of paint or polymer flooring.
Application features: temperature should be from 0 ° C to 17 ° C, air humidity not lower than 70%. If the humidity is lower, it should be moistened artificially - with electric humidifiers or by hanging wet rags in the garage, constantly making sure that they do not dry out. Only under these conditions will polymerization be good.
Epoxy primers
This type of impregnation consists of two components that are mixed immediately before use. You can work with them at temperatures above + 5 ° C, there are no other requirements. The cost is higher than that of polymer - $ 7 per kg, consumption is almost the same.
Concrete paints
Special concrete paints can be applied over the primer. They last for a long time - with these compounds they paint the floors in service stations, garages, etc. These are far from ordinary paints, but multicomponent compositions based on polymers, to which coloring pigments are added. You need to choose depending on the tasks that the floor covering in the garage should perform:
- Suitable for dedusting are PVC-based concrete paints.
- Polyurethane paint is suitable for protection against acids, alkalis and other aggressive substances.
- Increased strength, abrasion resistance - two-component epoxy paints.
If we talk specifically about garages, then epoxy compounds are probably more suitable. They create a strong film that adheres very well to the concrete base. This paint does not swell or fly around. Over time, it can rub a little, and then in places of very heavy load. It can be used in service stations, basements and garages.
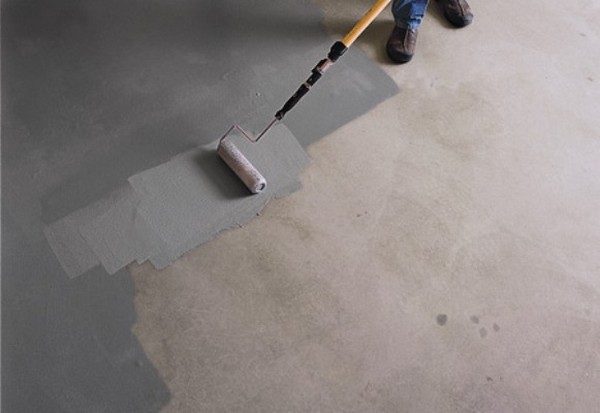
Concrete paint will simultaneously remove dust, give an attractive appearance, and reduce moisture absorption
Epoxy concrete paint is applied to the prepared concrete base. The floor must be dry (at least 30 days must elapse from the moment of pouring). If the screed has been poured recently, the cement laitance is removed from the surface with a stiff (steel) brush. If the floor is old, there are chips and cracks, repair them, remove grease stains. Remove debris after processing.
Before applying the paint, the floor is washed with PVA diluted with water. The second option is a weak aqueous solution of hydrochloric acid (1: 9). After a day, the surface is cleaned with a vacuum cleaner or a soft brush. the concrete floor is then ready for epoxy paint application.
The base and hardener are brought into a warm room per day. The temperature must be above 18 ° C. Mix each of the components separately, in their own container. Then a hardener is added to the container with the base at the rate and the composition is mixed. If necessary, you can use the solvent specified in the instructions. The viability of such a paint is small (time to hardening), therefore it is necessary to work quickly.
Rubber paint
This type of paint has increased waterproofing characteristics, good hiding power, high wear resistance, it is easy to wash, it is possible even with the use of detergents, it is resistant to alkalis. It can be used at temperatures from -50 ° C to + 60 ° C. When painting, it creates a coating very similar to rubber, with practically the same properties. There are also disadvantages - the surface is too smooth and can be slippery in winter. The second unpleasant moment, when the car drives into the garage and slips a little, the wheels can tear off pieces of paint. The way out is to put rubber bands under the wheels. the most popular option is from the conveyor. They do not wear out for years, and they will coexist perfectly with rubber paint.
Surface preparation consists in removing old flaking coatings, chalk, dust, grease stains. If the floor has a glossy finish, sand it to a matt finish. The last step is to wash the floor with a soda solution, then rinse with water and dry.
It is necessary to apply paint in 2-3 layers.Stir before use, it is not recommended to dilute, but as a last resort, you can use the solvent specified in the instructions. Stir the paint regularly during use.
Rubber floor covering in the garage
Rubber flooring will be comfortable and practical. Its disadvantage is a solid price - from $ 18 per square meter, if we talk about a modular rubber coating.
Today the rubber cover is available in three versions:
- modular plates of different sizes;
- roll rubber covering;
- rubber crumb with polymer binder.
Rolled and modular covering differs in the type of laying and the form of release. The rest of the characteristics are similar. The method of installation practically does not differ, only in one case the coating is assembled from fragments, most often of a square shape, with the edges decorated in the form of locks of different configurations. The roll cover is rolled out on the floor. Both types are glued with polyurethane adhesive. Concrete preparation is standard: sealing chips and dents, removing dust and dirt, primer (polymer impregnation).
When choosing modular or roll rubber cover, pay attention to the thickness of the rubber. It can be from 4 mm to 50 mm. A very thick floor covering in the garage is not suitable for him, but also too thin can be damaged by the wheels. The optimum thickness is 10-15 mm. This is not very expensive for the price, and more than enough in terms of characteristics.
Rubber crumb or they say also rubber asphalt is a two-component coating. The crumb itself comes in bags and is black. There are dyes to give it a different color. They are added to dry crumbs and mixed until completely colored. Then the binder is added. This is usually a polyurethane adhesive. The mass is stirred until smooth. But the process must be fast - the hardening time is very short. The crumb with polyurethane is spread on a prepared base (leveled, primed, covered with a layer of polyurethane glue), leveled and pressed with a roller.
PVC tile
This type of flooring has appeared recently, it is made from polyvinyl chloride (PVC) with various additives. There are both options for home (PVC laminate) and for technical and industrial premises. If we talk about properties, the PVC tile floor covering in the garage absorbs sounds, makes the floor warmer, is not afraid of the effects of gasoline, solvents, acids, fats, alkalis, is completely waterproof, durable. The price is comparable to the cost of commercial linoleum.
According to the method of laying, there are two types of PVC tiles - a modular covering, which is simply connected with locks and is not attached to the base, and a covering that is glued to polymer glue. For laying, a flat base is required with differences of no more than 5 mm / m2... This is perhaps the only drawback of this material: such a flat floor in the garage is more the exception than the rule.
Tile garage floor
Quite understandable, but not the best choice. First, debris constantly accumulates in the seams. Secondly, the coating is slippery, unless you take a special tile with an anti-slip surface, but it is expensive. Thirdly, from the fall of heavy objects, the tile breaks. Nevertheless, the floor is made of tiles in the garage, because there are also advantages: it is easy to clean, the well-known laying technology.
If we talk about the choice of tiles, the best option would be technical porcelain stoneware. It is not as beautiful as decorative, but also more democratic at a price. Its unpolished surface is non-slip, it is installed according to the usual technology for tiles. You can only try to make fewer seams so that there are fewer problems with them.
There is a very inexpensive option for finishing the floor in the garage with tiles - buy a fight and make a "mosaic".True, such artistic work will take more time, but tile battle is sold for almost nothing.
Self-leveling floors
Very good technical characteristics and appearance have Self-leveling floors... They are very resistant to external influences, strong and durable. Their disadvantage is a very rather big price. Especially for polymer and epoxy. The third type - concrete self-leveling floors - has a more affordable price. It is usually used to make a durable and dust-free garage floor covering.
They got their name due to the fact that they have a liquid consistency and spread over the base. These compounds are also called self-leveling, since, due to their high fluidity, they are distributed over the surface. But do not think that they should not be leveled at all. Having poured the composition in one place, it is necessary to "disperse" it with a spatula or some similar instrument over the surface, more or less evenly distributing it. Finally, the solution will even out by itself, but the degree of fluidity is different for different compositions, but manual distribution will never hurt (usually expensive brands spread better).
This type of garage flooring requires a flat, primed base. The primer is selected on the same basis as self-leveling floors. Since the finishing compound is not cheap, they try to level the base as best as possible - in order to reduce the consumption of the self-leveling floor.
Choosing a floor covering in a garage is not easy - there are many materials that meet the requirements. The only thing that can stop you is a limited budget and the need to have an even foundation (also requires considerable expenses). From this point of view, the most democratic option is impregnation and paint for concrete.